Notre blog
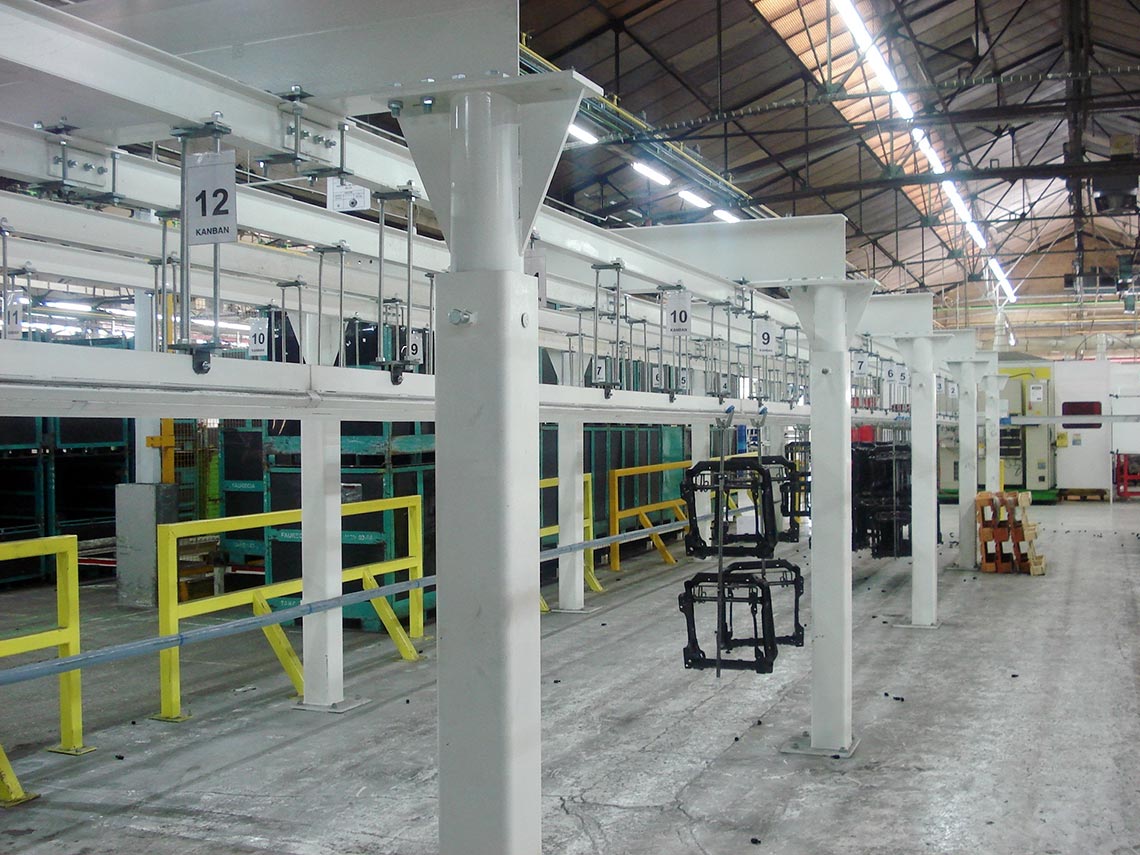
La sécurité des opérateurs et des lignes de production : priorité n° 1
La sécurité des opérateurs sur les lignes de production est aujourd’hui considérée comme la priorité n° 1, notamment dans les secteurs exigeants tels que la fonderie et la production de verre creux. Mettre des lignes en totale sécurité, que ce soit par le biais de nouveaux investissements ou d’opérations de chantiers de modernisation et de mise en conformité aux normes, est une opération délicate et coûteuse qui requiert compétence et professionnalisme. Découvrez les 4 étapes indispensables que votre prestataire spécialisé doit absolument respecter.
Étape n° 1 : l’audit
Afin d’évaluer l’ampleur des actions à mener et les normes particulières devant être respectées, une phase d’audit terrain doit impérativement être menée, posément et de manière exhaustive.
Dans le domaine de la sécurité des machines, le point de départ est la norme, dont l’esprit doit absolument s’imposer à chaque étape de conception, de développement ou de rétrofit, d’installation et d’utilisation d’un équipement.
La norme européenne (Directive Machines 2006/42 CE) doit être respectée mais il convient d’aller plus loin, surtout pour les sites de production complexes. Il est important de s’adapter à la réalité industrielle, dans un contexte où les métiers sont très différents les uns des autres et affichent tous des spécificités. Les compétences et le savoir-faire des équipes en place sont déterminants.
Étape n° 2 : l’analyse de risque et l’analyse fonctionnelle
Cette phase consiste à décomposer toutes les fonctions du système, de la machine ou du process, et à analyser les risques pouvant survenir lors du fonctionnement normal. Mais pas seulement, toute la richesse et l’intérêt de cette étape consistent à élaborer des scenarii de fonctionnement dégradé, en surcharge, pour prévoir les aléas et à contrer leurs impacts sur la production et sur le comportement des opérateurs, dûment formés.
Étape n° 3 : l’AMDEC
L’analyse fonctionnelle conduit habituellement à une réflexion profonde et à l’établissement d’une AMDEC (Analyse des modes de défaillance, de leurs effets et de leur criticité). Cette dernière permet de figer un plan d’actions et des priorités.
Cette méthode permet de fouiller dans le fonctionnement du système analysé et, par le biais d’une grille de notation, de fournir des informations multiples telles que :
- La liste des pièces de rechange et des consommables, dont la disponibilité est indispensable pour assurer la continuité des productions,
- Les éventuels besoins de formation complémentaire des équipes de production en présence et à venir,
- Les plans de contrôle périodique,
- Les fréquences d’entretien,
- Les plans de maintenance préventive et systématique.
Étape n° 4 : Cahier des charges et plan d’actions
Enfin, le plan d’actions est défini avec des mises en conformité à réaliser en priorité sur les équipements. La rédaction d’un cahier des charges détaillé permet de lancer une consultation auprès de plusieurs fournisseurs.
Ces cahiers des charges peuvent porter sur tous les aspects d’un système :
- Structure,
- Mécanique,
- Automatismes,
- Ergonomie.
Besoin d’un spécialiste pour sécuriser vos lignes de production ?
- Acteur reconnu dans le domaine de la maintenance industrielle, TSI Ingénierie développe une activité importante dédiée à la sécurité des lignes de production. Dans le cadre de sa démarche, l’entreprise porte attention à tous les niveaux de sécurité, que ce soit pour répondre à une demande d’améliorations ou dans le cadre de la mise en conformité d’une installation.
- TSI Ingénierie propose systématiquement une phase d’audit à ses clients, suivie de l’analyse des risques, de l’analyse fonctionnelle et éventuellement d’une AMDEC. Dans certains cas, TSI Ingénierie se fait accompagner par un organisme agréé (ex : Apave ou Dekra) chargé de valider les interventions techniques de la société. Un plan d’actions détermine ensuite les mises en conformité à réaliser en priorité sur les équipements.
- Certifiée MASE (Manuel d’Amélioration de la Sécurité des Entreprises), l’entreprise s’appuie sur un savoir-faire de plus de 30 ans en maintenance industrielle et sur une équipe de 80 spécialistes en mécanique, chaudronnerie, électromécanique, hydraulique, pneumatique, entre autres. Pour la partie dédiée aux automatismes, TSI Ingénierie travaille avec un partenaire.
Obtenez davantage d’informations.